MAI Tank – Entwicklung eines rationellen Fertigungsverfahrens für neuartige Drucktanks aus Faser-Thermoplast-Verbunden für die Luftfahrtindustrie
Neuartige Drucktanks aus carbonfaserverstärkten Kunststoffen für Feuerlöschsysteme in der Luftfahrt
Projektpartner
Apparatebau Gauting GmbH, Voith Composites GmbH & Co. KG
Laufzeit
01.10.2014 – 31.03.2017
Fördergeber
Bundesministerium für Bildung und Forschung
Motivation
Das seit vielen Jahren in Frachträumen von Flugzeugen eingesetzte Löschmittel wird aufgrund seiner Umweltgefährdung ab 2018 für neu zugelassene Flugzeuge verboten. Alternativ soll Stickstoff in Verbindung mit Wassernebel eingesetzt werden. Zur Speicherung des Stickstoffs werden daher leichte Drucktanks benötigt. Im Rahmen des Forschungsprojektes MAI Tank solltn neuartige Drucktanks aus carbonfaserverstärkten Kunststoffen entwickelt und untersucht werden. Dabei stand der effiziente Herstellungsprozess mit Faser-Thermoplast-Verbunden im Fokus der Arbeiten. Der Ansatz der sequenziellen Bauweise von Drucktanks, der in dem Projekt StorHy bereits untersucht wurde, wurde in diesem Projekt teilweise aufgegriffen und weiterentwickelt. Neu war dabei insbesondere der Einsatz eines Schleuderprozesses zur Herstellung eines Typ 5 Tanks. Im Vergleich zu bisher am Markt verfügbaren Drucktanks kann damit zum einen das Herstellverfahren effizienter und zum anderen der Einsatzbereich aufgrund eines modularen Aufbaus des Behälters vergrößert werden. Ein weiterer Vorteil des neuen Fertigungsverfahrens liegt darin, dass die erforderliche Abdichtungsschicht in einem Arbeitsschritt mit dem Zylinderrohrlaminat verbindbar ist.
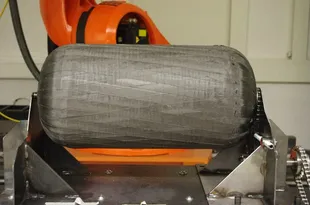
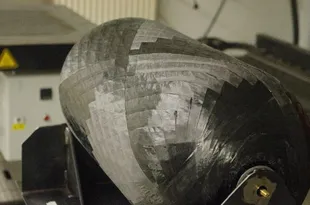
Vorgehen
Für die Auswahl eines geeigneten Tapematerials wurden zunächst Tapeproben verschiedener Hersteller beschafft und eingehender untersucht. Hierfür wurden Schliffproben hergestellt und die Oberfläche der Materialien charakterisiert. Für die Ermittlung von geeigneten Prozessparametern wurden Legeversuche auf der AFTP-Anlage des TUM-LCC durchgeführt. Ziel dieser Versuche war die Ermittlung von Prozessparametern (Temperatur, Geschwindigkeit, Anpressdruck), bei denen eine vollständige Konsolidierung der Tapes sichergestellt ist. Zur Quantifizierung der Konsolidierungsqualität wurden Keil-Schälversuche (engl.: Wedge-Peel Tests) durchgeführt. Anschließend musste die AFTP-Anlage für die Fertigung des thermoplastischen Tanks modifiziert werden, um eine vollständige Umwicklung der Boss-Teile (seitliche metallische Anschlüsse) zu ermöglichen und um Kollisionen mit dem Tank bzw. der Wickelachse zu vermeiden. Basierend auf dieser Analyse der Anlage wurde zum einen eine neue Andruckrolle konstruiert und zum anderen eine freistehende Wickelvorrichtung entworfen und in Betrieb genommen. Im nächsten Schritt, der Programmierung, wurden Ablagepfade in Cadwind® erstellt. Während der anschließenden Fertigung des Tanks erfolgte das Aufbringen der Umfangslagen problemlos. Die gewählten Prozessparameter führten zu einer sehr guten Lagenkonsolidierung. Nach dem Aufbringen der Umfangslagen wurden verschiedene Kreuzlagen auf den Liner und die zuvor gelegten Umfangslagen aufgebracht. Die Kreuzlagen dienten einerseits der axialen Versteifung des Behälters. Andererseits wurden die Kreuzlagen über die beiden Polkappen des Behälters geführt und stabilisierten die metallischen Boss-Teile im Liner. Beim Wickeln von Kreuzlagen mit einem Winkel von 10° relativ zur Behälterlängsachse wurden jedoch Spalte zwischen Boss-Teil und Laminatansatz identifiziert.
Folgende Ursachen für die Spaltbildung wurden ermittelt:
- das Prinzip der ATP/AFP Technologie
- das Verhältnis der Legekopfgröße zur Bauteilgröße
- die Gestaltung des Boss-Teils/des Behälters.
Für die Bewertung des Thermoplastkonzeptes wurde durch den Partner Voith ein Berstversuch durchgeführt. Der Tank versagte bereits bei einem Druck von ca. 150 bar katastrophal. Dies war bedeutend weniger als der Auslegungsdruck von ca. 900 bar. Der Berstversuch zeigte, dass das Boss-Teil aus dem Laminat gedrückt wurde. Dieses Schadensbild bestätigte die Vermutung aus der Prototypenanalyse, dass das unvollständig belegte Boss-Teil die Schwachstelle des Tanks darstellt. Die Linergeometrie sowie die Gestaltung der Boss-Teile basierten auf einer gängigen Lösung für Nasswickellaminate. Für den ATP-Prozess stellt das Design somit lediglich eine Kompromisslösung dar. Zwei grundlegende Ansätze sind bei einer Umgestaltung des Tanks denkbar:
- Fertigungsgerechte Gestaltung der Boss-Teile:
Dabei sollte eine bessere Zugänglichkeit der Boss-Teile mit dem Tapelegekopf gewährleistet werden. Bei einer besseren Zugänglichkeit kann das Boss-Teil ähnlich wie beim Nasswickeln vollständig mit Tape belegt werden. - Strukturmechanische Überarbeitung des Boss-Teils:
Unter der Prämisse, dass das Boss-Teil nicht vollständig belegt werden kann (z.B. aufgrund von Limitationen des Legekopfes), muss das Boss-Teil so gestaltet werden, dass die Last durch den Innendruck trotz unvollständiger Belegung aufgenommen werden kann.
Publikationsliste
Schäfer, P.M.; Guglhoer, T.; Sause, M.G.R.; Drechsler, K.: Development of intimate contact during processing of carbon fiber reinforced Polyamide-6 tapes. Journal of Reinforced Plastics and Composites, 2017, 1 – 15
Schäfer, P.M.; Gierszewski, D.; Kollmannsberger, A.; Zaremba, S.; Drechsler, K.: Analysis and improved process response prediction of laser- assisted automated tape placement with PA-6/carbon tapes using Design of Experiments and numerical simulations. Composites Part A: Applied Science and Manufacturing 96, 2017, 137-146
Schäfer, P.M.; Kreuzhage, S.; Zaremba, S.; Drechsler, K.: Experimental Investigation of inter-layer thermal contact resistance and its relevance for consolidation of thermoplastic composites. ECCM17 - 17th European Conference on Composite Materials, 2016
Schäfer, P.M.; Staden, M.; Zaremba, S.; Drechsler, K.: Material characterization for determining the consolidation properties of carbon fiber tapes with PA 6 matrix. ICCM-20 - 20th International Conference on Composite Materials, 2015
Danksagung
Der Lehrstuhl bedankt sich für die Förderung des Projektes „Entwicklung eines rationellen Fertigungsverfahrens für neuartige Drucktanks aus Faser-Thermoplast-Verbunden für die Luftfahrtindustrie – MAI Tank“, die vom Bundesministerium für Bildung und Forschung über den Spitzencluster MAI Carbon gewährt wurde (Förderkennzeichen: 03MAI24C).

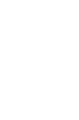

Ansprechpartner
Dipl.-Ing. Kalle Kind; Dr.-Ing. Swen Zaremba
Abschlussbericht
Externer Link (pdf)