DEfcodoor – Entwicklung eines umweltfreundlichen letzten Konsolidierungsschrittes für eine Helikopter Tür unter Nutzung von thermoplastischer Faserlegetechnik
Die Herstellung von Hubschrauberkomponenten aus Verbundwerkstoffen ist ein besonders energieintensiver Prozess. Neuartige laserbasierte Verarbeitungsverfahren eliminieren die Notwendigkeit des Einsatzes des energiehungrigen Autoklavprozesses und bieten darüber hinaus weitere Vorteile.
Projektpartner
Dutch Thermoplastic Components B.V., AFPT GmbH
Laufzeit
01.09.2011 – 31.07.2013
Fördergeber
FP7-JTI – Spezifisches Programm „Zusammenarbeit“: Gemeinsame Technologieinitiativen der Europäischen Union
Motivation
Hochleistungsverbundwerkstoffe für Hubschraubertüren liefern ein geringes Gewicht und hohe Festigkeiten bei gleichzeitiger Recycelbarkeit. Jedoch benötigen konventionelle Verarbeitungsverfahren für duroplastische Verbundwerkstoffe einen einergieintensiven Prozessschritt zur Aushärtung von früher per Hand abgelegtem Prepreg-Material im Autoklaven. Im Projekt DEfcodoor entwickelten Wissenschaftler eine Technologie zur Verbesserung der Nachhaltigkeit bei der Produktion von Hubschraubertüren. Sie nutzt thermoplastisches Prepregmaterial und das laserbasierte thermoplastische Faserlegeverfahren (TFP). TFP ermöglicht eine hohe Materialablagerate bei in situ Konsolidierung der thermoplastischen unidirektionalen Tapes und eliminiert dabei die Notwendigkeit verschiedenster Fügeschritte. Der Verzicht auf den Autoklaven reduziert ebenfalls die Produktionszeit je Komponente. Thermoplaste haben gegenüber Duroplasten etliche Vorteile und gewinnen deshalb stetig an Boden. Thermoplaste benötigen beispielsweise keinen Autoklaven zur Aktivierung der Ausbildung chemischer Vernetzungen. Da formgebende Prozesse reversibel sind, können sie eingeschmolzen und wiederverwendet warden. Schließlich ist ihre Fertigung umweltfreundlicher als die Fertigung duroplastischer Kunststoffe, da letztere besonders energieintensiv ist und schädliche Chemikalien emittiert.

Vorgehen
Das Team entwickelte einen Herstellungsprozess für Helikopterstrukturen aus Außenhaut und Versteifungselementen. Angepasste Laminate für die Versteifungselemente mit lokalen Verstärkungen wurden durch das laserunterstützte TFP hergestellt und mit Hilfe des Thermoformprozesses in Omega-Form gebracht, um in Helikoptertüren angewendet werden zu können. Die Omega-Profile wurden in situ, wiederum mit der Lasertechnologie, mit den Außenhautelementen gefügt. Die Wissenschaftler verglichen die Eigenschaften der in situ konsolidierten Bauteile mit den konventionell gefertigten, nachkonsolidierten Bauteilen. Das Projekt DEfcodoor demonstrierte somit die vielen Vorteile laserbasierter Thermoplastverarbeitung und nachfolgendem Thermoformen für die Herstellung von strukturellen Helikopterbauteilen. Der Prozess reduziert nicht nur Energieverbrauch und Materialabfall. Der Abfall kann auch für die Herstellung kleinerer Bauteile wiederverwendet werden. Durch die Eliminierung von nachträglichen Fügeprozessen durch die in situ Konsolidierung konnten die Montagekosten um etwa 40 % reduziert werden. Die kontinuierliche Verbesserung des Prozesses hinsichtlich Produktqualität eröffnet die Möglichkeit für diese Technologie, einen wichtigen Beitrag für die Sicherung der Wettbewerbsfähigkeit und Nachhaltigkeit der Hubschrauberindustrie zu leisten.
Publikationsliste
Radlmaier, V.; Ehard, S.; Ladstätter, E.; Drechsler, K.: Thermoplastic Automated Fiber Placement - Current Fields of Application and Future Prospects. JEC Composites Magazine (97), 2015, pp. 39-45
Radlmaier, V.; Obermeier, G.; Ehard, S.; Kollmannsberger, A.; Körber, H.; Ladstätter, E.: Interlaminar Fracture Toughness of Carbon Fiber Reinforced Thermoplastic In-situ Joints. Polymer Processing Society Conference (PPS) 2015, 2015
Radlmaier, V.; Henne, F.; Ladstätter, E.: Novel environmentally friendly manufacturing approach for thermoplastic composite helicopter doors. Greener Aviation 2014 Conference, 2014
Danksagung
Dieses Projekt wurde im Rahmen von FP7-JTI – Spezifisches Programm „Zusammenarbeit“: Gemeinsame Technologieinitiativen der Europäischen Union unter der Finanzhilfevereinbarung Nr. 287103 finanziert (“Development of a Ecological friendly final consolidation step using Thermoplastic Fibre Placement for a helicopter door”). Diese Veröffentlichung spiegelt nur die Ansichten des Autors wieder und die Europäische Union haftet nicht für jegliche Verwendung die darin enthaltenen Informationen.
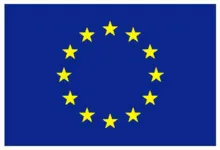
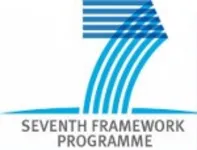
Ansprechpartner
Luciano Avila Gray, M.Sc.; Dipl.-Ing. Kalle Kind; Dr.-Ing. Swen Zaremba
Abschlussbericht
Download (pdf)