TOSCA - Erzeugung von ThermO- und fluiddynamischen Stoffdaten für CH4/LOX Antriebe
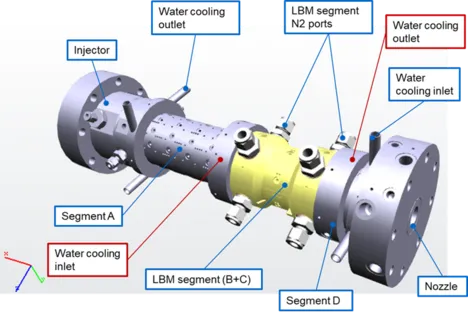
The oxygen/methane propellant combination has been intensively investigated for several years for future space applications. It is more environmentally friendly than storable propellants in particular and also offers technical and economic advantages. However, a number of technical and scientific issues still need to be clarified for safe and reliable application. Applications range from space transport and control systems to long-term missions.
In general, methane has several advantages over other common rocket fuels. Compared to hydrogen, it has a substantially lower specific impulse, but this is more than compensated for by the higher density and therefore much smaller tank mass. In addition, the higher temperature in the tank means that expensive helium can be dispensed with for pressurisation and purging tasks and cheap nitrogen can be used instead. Higher density and temperature also reduce the demands on the turbopump and seals. Compared to hypergolic fuels, methane is not only non-toxic and therefore much easier to handle, but also has a higher specific impulse, which is not fully utilised even when the lower density is taken into account. The same applies to longer hydrocarbons, which also have the disadvantage of a higher tendency to form soot. Not to be forgotten is the fact that methane has ISRU (In-Situ Resource Utilisation) potential. Methane has been found on a number of objects in our solar system (including Mars, Titan and Uranus). It is therefore conceivable in principle to fly a spacecraft to one of these celestial bodies, carry out a scientific mission and at the same time refill the methane tanks in order to return to Earth.
A major advantage of using methane as a rocket fuel is the low production costs. However, this only applies if liquefied natural gas (LNG) is used, which is generally traded in two different versions. A mixture known as ‘rich LNG’ with up to 8% ethane and a methane content of slightly less than 90% and a mixture known as ‘lean LNG’ with a methane content of almost 98%. It should also be noted that the concentrations are average values and the individual values can vary considerably depending on the supplier. Better qualities are commercially available, methane 2.5 or 3.5 with 99.5% or 99.95% methane or even higher concentrations, which then already have food quality and are correspondingly expensive. In principle, it is advantageous to keep the carbon content as low as possible, as the reduction in the molecular weight of the combustion products leads to higher efficiency.
Although CH4/O2 engines are being developed worldwide, there is currently no airworthy carrier system that uses these fuels. One reason for this is the insufficient knowledge of the specific thermodynamic and fluid dynamic properties of the methane mixtures. Of particular importance are their changes in the environment of the critical states (pressure, temperature), as these are design drivers for both the cooling system and the injection system. Design tools for these systems must contain sufficiently validated models for heat transfer and fuel atomisation, as this is the only way to carry out reliable design studies. Although preliminary work has already been carried out in this direction, detailed modelling and its validation using high-quality numerical methods (direct numerical simulation) and corresponding test data and its subsequent industrialisation, i.e. the transfer of a scientifically sound calculation tool into an industrially applicable tool, is still pending.
The national space programme reflects the core objectives of the German government's space strategy. This project contributes to this strategy by establishing detailed knowledge of the thermophysical properties of commercially available liquid gas, testing classical methods of turbulence modelling and heat transfer in additively manufactured and thus specifically rough cooling channels and conducting experiments to determine the heat transfer in such combustion chambers.
The problems addressed in the project have two main objectives. To expand the expertise of the Technical University of Munich in the field of thermophysical determination of material data of commercially available liquefied natural gas (LNG) and the modelling of heat transfer and cooling in cooling channels with deterministic roughness. Development of models with which industrially used design tools can be used to design additively manufactured cooling channels.
In this way, an active contribution will be made to the implementation of the German space strategy and the preservation and expansion of German core competences in the Ariane programme will be consolidated. Improved design methods will facilitate the use of 3D printed components of the European launchers and thus secure German competitiveness, particularly in the propulsion sector.
SCIENTIFIC AND TECHNICAL OBJECTIVES OF THE PROJECT
The scientific and technical objectives of the TOSCA project are aimed at further expanding the existing knowledge and expertise at the Technical University of Munich in the field of thermodynamics of cryogenic propellants, modelling of combustion, heat transfer and cooling of liquid rocket engines. In addition, the prediction accuracy of existing commercial calculation methods for predicting the heat transfer on the coolant side is to be improved. To this end, appropriate models must first be developed and validated using high-quality numerical methods and comparison with experimental data. In addition to model validation, the experiments to be carried out also serve to qualify additive manufacturing processes and to address issues relating to the prediction of the service life of components manufactured in this way.
Specifically, the technical work programme of the TOSCA project addresses the following technology fields and objectives:
1. Determination of the thermo-physical parameters of commercially available light liquefied gas (‘lean’ LNG):
Small foreign components in LNG, such as hydrogen, argon, nitrogen, carbon dioxide, water or other hydrocarbons such as ethane, propane and butane, have only a minor influence on the performance of the engine, but can have serious consequences for cooling. These foreign components can significantly change thermo-physical properties that are extremely important for cooling, such as viscosity, thermal conductivity and in particular the heat capacity, especially in the immediate vicinity of the critical state. Another problem is that the position of the critical state (pressure and temperature) also shifts depending on the composition.
The aim is to develop correlations for cooling channels, injection elements and ignitions that allow the calculation of relevant material data for ‘lean LNG’ mixtures in the near-critical pressure and temperature range as well as the development of a corresponding multidimensional database.
2. Adaptation and validation of calculation methods for the prediction of coolant-side heat transfer in LNG-cooled combustion chamber segments:
Classical commercial calculation methods for predicting coolant-side heat transfer are generally sufficiently accurate to design reliable cooling systems.However, this no longer applies to mixtures of fluids with very different material properties.Especially in the area of transcritical operating conditions and for extremely high thermal loads in cooling channels of rocket combustion chambers, the accuracy of prediction is no longer guaranteed.
It is also unclear to what extent the increase in wall roughness, which can hardly be avoided by additive manufacturing processes, and the resulting increase in near-wall turbulence can be modelled using conventional eddy viscosity methods.
The aim is therefore to characterise the application limits of classical calculation methods and to improve them through appropriate model modifications and validation.
3. Experimental investigation of heat transfer and cooling as well as comparison of conventionally and additively manufactured combustion chamber segments:
The planned combustion chamber tests in a combustion chamber pressure range between 40 - 80 bar serve to determine the heat transfer of various additively manufactured combustion chamber segments with targeted wall roughness.The aim is also to determine the pressure loss in the cooling channels in order to be able to better evaluate the expected improved cooling, taking into account the increased pressure loss compared to smooth walls.The data obtained will be used to expand calculation methods for rough cooling channels and to validate models for predicting service life.