High Speed Research Compressor
Project History
HSRC is the largest compressor test rig at the LTF and has been operated in cooperation with GE Aerospace since 2016. Its unique design enables the experimental investigation of the high-pressure compressor rear stages in a scaled test rig under engine-representative flow conditions.
Test Rig
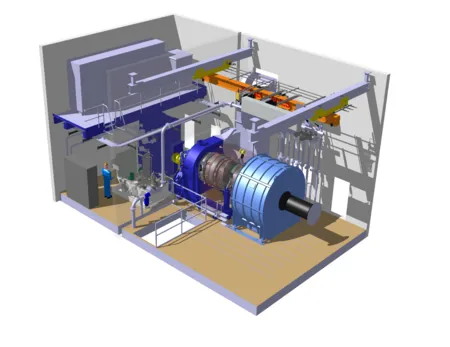
The 3.5-stage axial compressor is driven by a 3 MW electric motor. A maximum rotational speed of 5,000 rpm is achieved via a gearbox with a ratio of 1:2.52. A mass flow of up to 30 kg/s through the compressor can be achieved.
The mass flow is measured via an in-situ calibrated inlet. A settling chamber with a diameter of approx. 3 m ensures a homogeneous inlet flow to the compressor.
The compressor can be throttled to stall, where transient pressure sensors trigger a fast opening of the throttle to avoid structural loads on the test rig.
The secondary air system (SAS) allows control of the leakage flows through the rotor seals. In addition, the controlled cooling of the rotor and the double-shell casing allows the rotor gap to be adjusted on a small scale. To stabilize the compressor, bleed air can be taken from rotor 3.
The exhaust gas, which can reach temperatures of up to 200 °C, is discharged into the environment via a silencer.
Instrumentation
Permanently installed sensors
A large number of permanently installed sensors are used to analyze the compressor and monitor test bench operation. These are used to monitor the operating point and determine efficiency as well as to ensure safe operation. The efficiency of the compressor is determined via the pressure and temperature ratio between the inlet and outlet as well as via torque and speed measurement on the drive shaft.
Among other things, the following are used:
- approx. 600 Scannivalve pressure sensors (various measuring ranges)
- approx. 300 temperature sensors (NI, with own cold junction)
- approx. 30 transient housing pressure sensors (Kulites)
- approx. 700 acceleration, proximity and other sensors
- Torqmeter for speed and torque measurement
- MTU BSSM for monitoring the rotor clearance
- 3 ambient pressure sensors
- Rotor data telemetry system
- Up to 75 strain gauges for vibration monitoring on rotors and stators
A total of more than 1,600 measuring channels are available.
Traversable instrumentation
Up to three flow probes can be installed behind each row of blades on the HSRC and traversed in three axes (radial, circumferential, rotation in yaw direction). The probes are selected according to the measurement requirements.
In particular, the possibility of unsteady measurement of the flow field at 48 kHz (pressure measurement, 4-sensor FRAP) and up to 100 kHz (temperature and mass flow density with 5 µm hot-wire probes) with representative Mach numbers and strong instationarity behind the rotors is a unique feature of the test bench.
Work
New concepts and technologies for stabilizing the rear high-pressure compressor stages under engine-representative Mach numbers are being tested at the HSRC. These investigations are carried out in close cooperation with GE Aerospace.
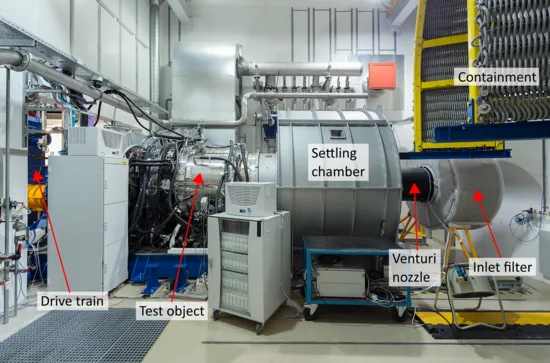
History
- 2013: Project start with definition of the design requirements for the compressor test bench
- 2015: Commissioning of the first subsystems
- 2016: First commissioning of the compressor at design speed, in-situ calibration of the inlet nozzle, verification of homogeneous inflow
- Since 2016: Annual test campaigns with continuous further development