SAINT
Contact: Jonis Kiesbye
Project Goals
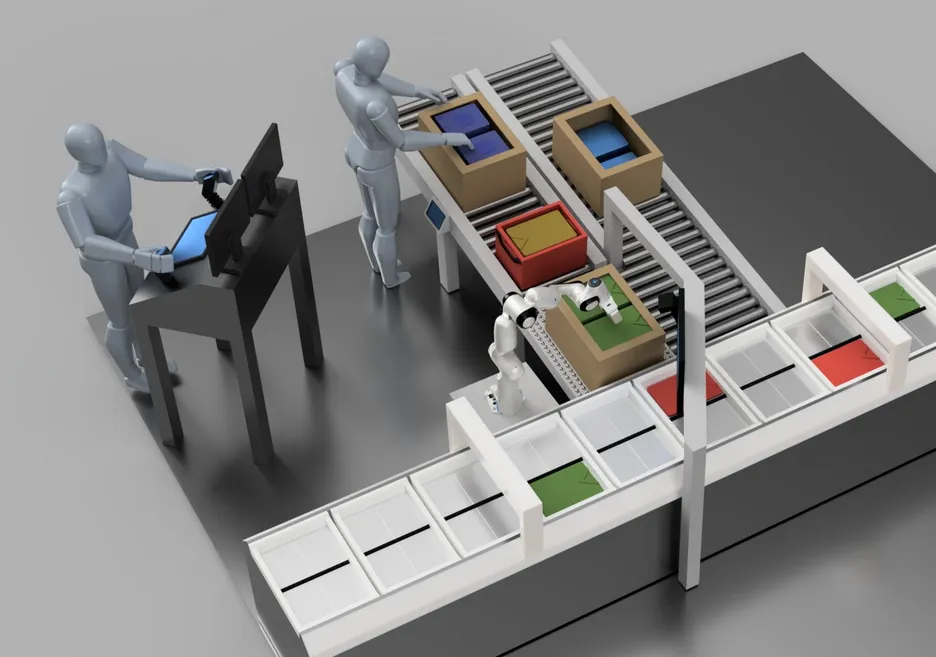
SAINT focusses on robotic bin picking in unknown environments. Industrial as well as extraterrestrial applications of robotic grasping have high reliability requirements that are not satisfied by the current state of the art.
Economic solutions for bin picking, the separation of chaotically distributed parts, are still rare and only found for well-known environments. The efficiency of humans and their low error rate can hardly be reproduced with robots for which, among other things, long calculation times of gripper poses and trajectories still cause severe problems. TUM’s chair for applied mechanics (AM) and Franka Emika GmbH are therefore developing advanced path planning and machine vision algorithms optimized at robotic bin picking.
TUM’s institute of astronautics (LRT) contributes a fault recovery and teleoperation module, which allows the robot system to recover from fault conditions autonomously or by incorporating input from a human operator.
FIEGE Logistik Stiftung, headquartered in Greven, is interested in innovative logistics solutions. In the context of this project, FIEGE provides the industrial usecase at one of its facilities.
Industrial Application
FIEGE is one of the largest logistics service provider in Europe und offers individual logistics solutions to its customers. At the facility in Mönchengladbach, FIEGE handles the logistics processing for a customer from the fashion industry. The range of automatically stored and sorted products spans clothing and other articles. Some processes like unpacking the items of clothing from cardboard boxes and placing them in drop boxes or on the split-tray sorter depicted above involve manual labor currently. This project aims to support these manual processes by using robotic arms. The research focus of the SAINT project is unpacking garments from cardboard boxes and placing them on a split-tray sorter. Our common goal is the productive application of robotics with relatively small modifications to the existing facility.
Shared Autonomy
We want to utilize the human operator’s time as efficiently as possible by augmenting the picking algorithms’ solutions with the human input to find a feasible solution to the fault that occured. The operator can focus on the cause of the fault and does not need to control the whole bin picking cycle in real-time.
Depending on whether the fault occurs during object detection, grasping, transport, or placement of the object, the teleoperation module selects the appropriate semi-autonomous app that allows the operator to efficiently provide the input needed for recovering from the fault condition.
The figure below shows an exemplary use case: If the robot system fails to detect an obstacle in the workspace autonomously, the operator can draw a keepout-sphere in the workspace to force the path planner to avoid the obstacle.
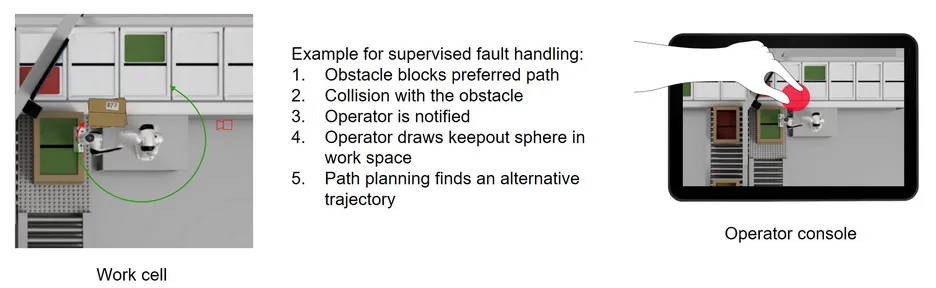
Fault Recovery
Autonomous fault detection, isolation, and recovery (FDIR) algorithms are commonplace in space vehicles. They ensure the availability of the satellite and its communication link in case of component failures. For the SAINT-project, we will adapt such algorithms to detect faults that happen during bin picking, estimate the possible consequences and evaluate whether to choose an autonomous or semi-autonomous recovery approach.
Student Theses
The SAINT project provides an interesting framework for writing your student thesis focusing on teleoperation, user interaction, fault recovery, ROS-software, etc.
Please have a look in the theses database of the FSMB and ask the SAINT contact person directly, which topics they have not published yet.
Projekt Partners
Chair of Applied Mechanics (AM) - Path planning
Franka Emika GmbH - Gripper and machine vision
Institute of Astronautics (LRT) - Fault recovery and teleoperation
FIEGE Logistik Stiftung & Co. KG - Industrial application
The SAINT-project is funded by the Bavarian research foundation (Bayerische Forschungsstiftung, BFS).