Aircraft Design (civil and military)
Research activities within the area of aircraft design range from the conceptual design of flying systems (manned or unmanned) to the prototype implementation and test of system demonstrators in ground and flight experiments.
Within the aircraft design activities new apporaches for system integration and the respective overall configurations are developed within an integrated conceptual design framework.
The range of configurations under investigation is from small UAV systems up to new transport solutions for civil and military air transport.
As future transport aircraft continue to evolve, the trend towards high aspect ratio wings is increasingly common, offering superior aerodynamic performance. These slender wings, however, introduce significant flexibility, which must be considered early in the aircraft design process.
Traditionally, aeroelastic modeling—integrating both aerodynamic and structural model—requires significant manual effort and specialized expertise, making early-stage evaluation complex and time-consuming.
To address this challenge, we target to develop the Flexible Aero Structural Toolbox (click here for more information). This in-house solution will streamline the aeroelastic evaluation process, reducing the modeling effort and improving efficiency for designers and engineers.
Kontakt | Fanglin Yu, Carlos Sebastia Saez |
Hydrogen as a sustainable alternative energy source for commercial aircraft holds promise for helping the aviation industry meet its climate goals. The transition to hydrogen and the relocation of fuel storage to the fuselage introduces a novel design space for wing structures and system integration. The Dry Wing Technology Exploration (DWiTE) project aims to explore this new design space by considering various disciplines—such as aerodynamics, structures, control and systems—to assess the overall benefits at the aircraft level. The scope includes, but is not limited to, hybrid laminar flow control, novel primary structure concepts, and internal kinematics. TUM’s contribution to the project focuses on developing innovative wing concepts that utilize active load control and assessing their impact on overall aircraft performance.
The project is funded under the grant of the German federal aviation research program LuFo VI-3 by the German Federal Ministry for Economic Affairs and Climate Action.
Kontakt | Fanglin Yu |
Partner | Bauhaus Luftfahrt e. V., RWTH Aachen, Technical University Hamburg |
The conceptual aircraft design has been used for years to develop new aircraft configurations or to evaluate new technologies in existing aircraft configurations. Up to now, different aircraft environments have been developed in industry and universities, showing a similar level of development but different competencies. With the objective to bundle the design expertise and the disciplinary knowledge of the German aviation universities and to make them usable in the long term, a common university-based aircraft design environment is being established within the project UNICADO. The fundamental goal is to exploit synergy potentials and to shift the focus in research and teaching from code development to actual design activities. The design environment will be validated together with industry and large-scale research. This will ensure connectivity with the design processes of industry and non-university research and thus enable efficient joint research in the field of aircraft design.
The project is funded under the grant of the German federal aviation research program LuFo VI-1 and 2 by the German Federal Ministry for Economic Affairs and Climate Action.
Partner | RWTH Aachen, Technical University Berlin, University Stuttgart, Technical University Hamburg, Technical University Braunschweig |
Associate Partner | Airbus SE |
Contact | Kristina Mazur, Tobias Weckenmann, Maren Huxel, Meric Taneri |
The combination of vertical take-off capability and aerodynamic forward flight results in an aircraft that can be used flexibly and enables new types of missions to be carried out. This project investigates the most important aspects of such aircraft. The mission parameters and operational areas are analyzed and corresponding configuration concepts for the different mission types are developed and evaluated. After this preliminary design the parameters of the most promising configuration is optimized for maximum mission performance. This detailed design is used to identify, construct and thoroughly test essential subsystems. Following the detailed design, prototypes of the aircraft are manufactured using the institute’s workshops and tested in flight tests. This means that a complete cycle in the aircraft design process is completed for each concept which is implemented. The focus is on unmanned aircraft with a maximum take-off weight of 5 kg - 150 kg. The main propulsion systems used are electrical systems (eVTOL UAV).
Contact | Thomas Seren, Moritz Thiele, Christian Rieger |
Aircraft design studies and optimizations require a flexible, user-friendly and extensible design environment to design both conventional and unconventional aircraft configurations and to accommodate innovative technologies. On this basis, the Institute of Aircraft Design develops an aircraft design environment for Conceptual Design and the early stages of Preliminary Design for use in research and teaching. It is based on the universal, object-oriented data model ADDAM (Aircraft Design Data Model), which is suitable for both transport aircraft and UAVs. For the individual subareas of aircraft design, an extensible collection of already existing as well as specially developed approaches and procedures is connected to the data model by means of a standardized interface. A library of aircraft, airfoils, engines and materials increases reusability and facilitates rapid exploration of various concepts.
Project site | ADEBO |
In the ProFla project, an aeroelastic process chain is being created which will enable small aircraft with high aspect ratio wings to be efficiently developed and safely certified at an early design stage. In addition to research into the unsteady aerodynamics of modern laminar airfoils, this includes in particular the development of a numerical tool chain and its validation through extensive ground and flight tests. For this purpose, suitable computational methods are implemented, which will allow an automatic adaptation of the simulation models to experimental results.
The project is funded under the grant of the German federal aviation research program LuFo VI-1 by the German Federal Ministry for Economic Affairs and Climate Action.
Contact | Carlos Sebastia Saez, Fabian Sturm |
Thanks to modern computer aided design and simulation tools, aircraft systems are being steadily improved. However, to ensure that reliability and performance requirements of the on-board systems are met, additional testing with the actual hardware is needed. The Iron Bird Test Facility offers a test environment for evaluating the functionality of the flight control system, avionics bus systems and the power distribution network amongst others. Dedicated electromechanical equipment allows for Hardware-in-the-Loop tests under specified conditions and recording of a wide range of operational parameters at high sampling rates.
Goals:
- Support the design and integration of on unmanned aerial vehicle research demonstrator aircraft
- Prepare unmanned aircraft for the implementation of novel aircraft system architectures
- Ensure functional and reliability specific requirements are met
Contact |
FLEXOP project, the predecessor of FLiPASED, was where the Institute has started its work in the field of multidisciplinary aircraft design. Created within the Horizon 2020 framework (funded by the European Union), the research work of the project was focused on aeroelasticity and flutter modelling, while the design team was responsible for overall design of the demonstrator used for testing the innovative active flutter suppression methods. The result was a 65kg, 7m wingspan UAV with interchangeable wing sets, each built to investigate a specific aeroelastic problem. The demonstrator went through flight testing, generating real-life data as a supplement for the simulations.
Building on this, the FLiPASED (Flight Phase Adaptive Aero-Servo-Elastic Aircraft Design Methods) project was launched within the same Horizon 2020 framework. The goal of the project is to further advance the methods in integrated aircraft design, coupling in between the areas of aeroelasticity, flight control methods, as well as certification and instrumentation. More than 10% fuel efficiency improvement and 20% reduction in peak amplitude of the gust response, as well as a 50% reduction of number of distinct models used during the development and certification process are set as project goals. The project will raise the efficiency of a currently separately existing development toolchains. It will develop methods and tools for very accurate flexible-mode modelling and flexible aircraft control synthesis, the accuracy of which will be validated using the FLEXOP UAV demonstrator. The results will be shared along with design requirements and standardized interfaces in an open source approach.
Partner | DLR, MTA SZTAKI, ONERA |
Contact | Dr. Christian Rößler, Julius Bartaševičius, Sebastian Köberle, Daniel Teubl, Fanglin Yu |
Modern sailplanes operate both at low speeds during circling in thermals and at high cruise-speeds in between. The goal is to achieve a high overall cross-country speed. The aerodynamic design is a compromise between the two flight conditions at two lift coefficients. By changing the shape of the wing, this compromise can be reduced. This can be achieved by conventional hinged trailing edge flaps. In the project MILAN, a morphing forward section is added to the flapped airfoil, which further increases the maximum lift coefficient within the laminar drag bucket in the morphed configuration. This allows to reduce the wing area and therefore the wetted surface, while keeping the same circling- and stall-speed. The maximum wing loading can be increased. As a result both the maximum lift-to-drag ratio and the high-speed performance are increased.
The project is funded under the grant of the German federal aviation research program LuFo V-3 by the German Federal Ministry for Economic Affairs and Climate Action.
Project Site | MILAN |
The European research project FLEXOP (Flutter Free FLight Envelope eXpansion for EcOnomical Performance improvement) aims to develop and validate new methods for designing active and passive systems for flutter suppression of very light and thus flexible wing structures. Under the guidance of the Horizon2020 research and innovation program, partners from industry and academia from 6 different countries are working on control algorithms, actuators, design optimization as well as an unmanned flying demonstrator with 7m wingspan and engine propuslion, in which the found approaches will be tested.
Partner | Airbus Innovation Works, DLR, FACC, INASCO, RWTH Aachen, MTA SZTAKI, TU Delft, University of Bristol |
Contact | sekretariat(at)lls.lrg.tum.de |
The idea of a virtual aircraft model, which allows virtual flight tests to predict aircraft loads and performance is part of the research project VitAM. The combination of structural and aerodynamic models with an application background on highly flexible wing structures to a unified coupled aeroelastic aircraft model is in research focus.
Partner | DLR, Airbus Defence&Space GmbH, Airbus Operations GmbH, Universität Stuttgart, TU Braunschweig |
Contact | sekretariat(at)lls.lrg.tum.de |
Recent Flight Control Systems (FCS) of commercial transport aircraft consist of highly optimized flight control surfaces, which are conventionally classified as primary or secondary – depending on their function and criticality. This mainly knowledge-based design with generally mono-functional allocation is often limited to small and local improvements under high effort. Consequently, various research studies present new technologies and concepts for functional enhancement of the FCS to increase the aircraft efficiency or performance during certain flight phases. Therefore, the aircraft design group developed a preliminary design methodology for advanced FCS with multifunctional flight control devices in early aircraft design phases. This integrated design approach includes the FCS configuration design, the FCS architecture design and the FCS mass estimation, within the framework of conceptual or preliminary aircraft design.
The aim of the MECC project, funded within the framework of the national aviation research programme, is to develop a minimal passenger cabin in terms of modularity and lightweight construction. In addition to the desired operational advantages, it is also important to save both costs and weight during the development phase.
Partner | Airbus GmbH, FERCHAU Engineering GmbH Geschäftsbereich Aviation, iDS Hamburg GmbH & Co KG, TÜV Rheinland AG |
Contact | sekretariat(at)lls.lrg.tum.de |
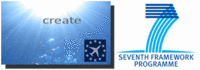
The aim of the project is to develop a process for identifying and promoting innovative concepts for the future, which are characterized by high potential benefits and high risks during implementation.
Partner | ASD, Ad Cuenta, Trevor Truman, ARTS, TUM, Bauhaus Luftfahrt, QinetiQ, NIVR |
Contact | sekretariat(at)lls.lrg.tum.de |
Sensitivity analysis of the fuselage cross-section for fuselage structure weight and mission performance.
Partner | Airbus Deutschland GmbH |
Contact | sekretariat(at)lls.lrg.tum.de |
Development of an Unmanned Aerial System for Low Cost High Resolution near Infrared Photography.
Partner | - |
Contact | sekretariat(at)lls.lrg.tum.de |
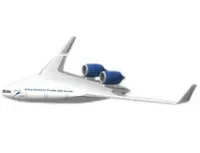
Design of a BWB (Blended Wing Body) and a CWB (Carry-through Wing Box Aircraft)
Partner | EADS IW, ONERA, Alenia |
Contact | sekretariat(at)lls.lrg.tum.de |

Design of a flying autonomous experimental vehicle.
Partner | EADS MAS, FSD, FH München |
Contact | sekretariat(at)lls.lrg.tum.de |
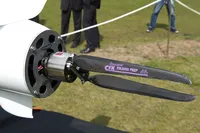
The Institute of Aircraft Design develops methods and models for the design and optimization of electric and hybrid propulsion systems within the aircraft design process.
Partner | - |
Contact | sekretariat(at)lls.lrg.tum.de |
In this research project, solutions are being developed which make electrical and hybrid propulsion architectures, which are already in use in general aviation, advantageously applicable to future commercial aircraft in a novel way.
Partner | - |
Contact | sekretariat(at)lls.lrg.tum.de |
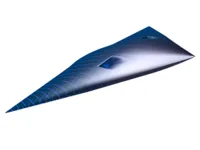
The project Sagitta, named after a stellar constellation, has been initiated by CASSIDIAN in 2011. A technology demonstrator with a low aspect ratio flying wing configuration is being developed by several institutes of the TUM, German research institutes and the industry in cooperation.
Partner | Cassidian, TUM AER, TUM FSD, TUM LLB, UniBw, DLR |
Contact | sekretariat(at)lls.lrg.tum.de |
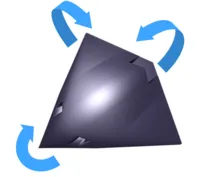
In this context, a technology concept is being developed for a low aspect ratio configuration without a vertical tail that achieves the desired control effect without moving components such as flaps.
Cassidian, TUM AER, TUM FSD, TUM LLB, UniBw, DLR
Partner | |
Contact | sekretariat(at)lls.lrg.tum.de |

The reduction of moving parts is interesting for thrust vectoring concepts to actively support flight control. In this field, new concepts will be investigated and developed, the technological maturity of which will be demonstrated on the flying demonstrator.
Partner | Cassidian, TUM AER, TUM FSD, TUM LLB, UniBw, DLR |
Contact | sekretariat(at)lls.lrg.tum.de |
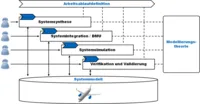
A part of the research area aircraft design is the analysis of model-based techniques for the improvement of the design process efficiency.
Partner | - |
Contact | sekretariat(at)lls.lrg.tum.de |
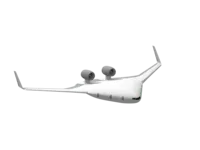
Design of a novel aircraft concept, the Blended Wing Body (BWB), a single-wing configuration with fuselage integration.
Partner | - |
Contact | sekretariat(at)lls.lrg.tum.de |
Design of unconventional unmanned configuration with a fuel cell propulsion system.
Partner | Boeing Research & Technology Europe |
Contact | sekretariat(at)lls.lrg.tum.de |
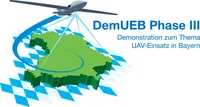
In the third phase of the DemUEB project, operational and technical solutions for the use of Unmanned Aerial Systems (UAS) for civil applications in Bavaria are being developed.
Partner | Unterbeauftragung: Cassidian Air Systems; Gesamtprojekt: Diehl BGT Defence, DFS, DLR, Cassidian Air Systems, EADS Innovation Works, Eurocopter, EMT, ESG, IABG, LLS, FSD |
Contact | sekretariat(at)lls.lrg.tum.de |