SensoTwin – Sensor-integrated Digital Twin for High-Performance FRP Applications
The fatigue behaviour of fibre-reinforced plastics (FRPs) is evaluated with respect to process-induced defects to determine the residual life of load-bearing structures of wind turbines using digital twins and a newly developed material ontology.
Project Partners
Deggendorf Institute of Technology – Technology Campus Hutthurm, Deggendorf Institute of Technology – Institute for Applied Informatics
Duration
01.02.2021 – 31.07.2024
Funding Authority
German Federal Ministry of Education and Research
Motivation
FRPs are widely used in the production of load-bearing structures of wind turbines. Under the influence of alternating loads within these structures, e.g. the rotor blades, the material undergoes continuous change. This is referred to as fatigue and can adversely affect the entire plant. As the boom in wind energy has waned in recent decades, the number of newly installed plants in Germany has been decreasing. In addition, an increasing number of plants will reach the end of their service life in the coming years. The digital tools elaborated in this project shall allow the prediction of the operational stability of FRPs and therefore ease the recertification, and with it, the continuation in service of wind turbines.
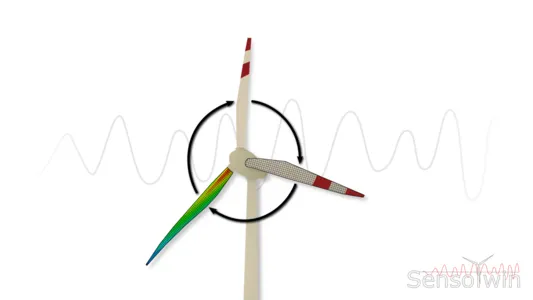
Method
As a basis for a lifetime material model, the fatigue behaviour of FRPs is experimentally characterised in terms of elasticity and strength under varying environmental conditions. From micromechanical testing of the composite constitutes to testing of a wind turbine blade root demonstrator, all necessary engineering parameters for the corresponding material model are determined. The knowledge gained is further used to create a multi-scale material model for FRPs, considering static strength and the operational stability. This holistic approach is subsequently transferred to the material ontology and then to the software application. The latter includes the prediction of process-induced defects based on process simulation and feeds its results through a mapping algorithm into the subsequent structural simulation. The use of uniform data exchange formats (e.g. HDF5) allows for additional input of real sensor data into the calculation routine. Finally, the model validations are carried out on the root demonstrator (a sensor-integrated twin of the digital model).
TUM-LCC acts as the consortium leader of this project in the framework of the MaterialDigital initiative. The chair focuses on the material characterisation as well as on the structural simulation while considering process-induced defects. Additionally, a validation of the calculated residual-life is carried out.
Acknowledgement
The chair thankfully acknowledges the funding provided by the German Federal Ministry of Education and Research in the initiative “Digitalisierung der Materialforschung in Deutschland – MaterialDigital” on a sensor-integrated digital twin for high-performance FRP applications (“Sensorintegrierter Digital Twin für Hochleistungs-Faserverbundanwendungen – SensoTwin”, funding code: 13XP5121A).

Contact Persons
Alexander Seidel, M.Sc.; Dr.-Ing. Swen Zaremba