MAI Hiras + Handle – Development of a Continously and Dynamically Loaded Component of a Vehicle Structure from Thermoplastic Carbon Fiber Composite Material and Exemplary Realization of a Motorcycle Rear Wheel Rocker
For the demonstrator part motorcycle rear wheel rocker, different types of load transfer elements were evaluated in an FE model and the bonding of metal inserts to fiber reinforced as well as injection molded parts was examined.
Project Partners
BMW AG, Automation W+R GmbH, Christian Karl Siebenwurst GmbH & Co. KG, EDAG GmbH & Co.KGaA, KraussMaffei Technologies GmbH, Frauenhofer Institut für Werkzeugmaschinen und Umformtechnik IWU
Duration
01.10.2014 – 31.03.2017
Funding authority
German Federal Ministry of Education and Research
Motivation
In the project MAI Hiras + Handle, the limits of carbon fiber reinforced materials should be explored and it should be examined in how far these limits are dependent on the fiber length. It also had to be examined how a superposition of different fiber systems can affect performance and properties of manufactured components.
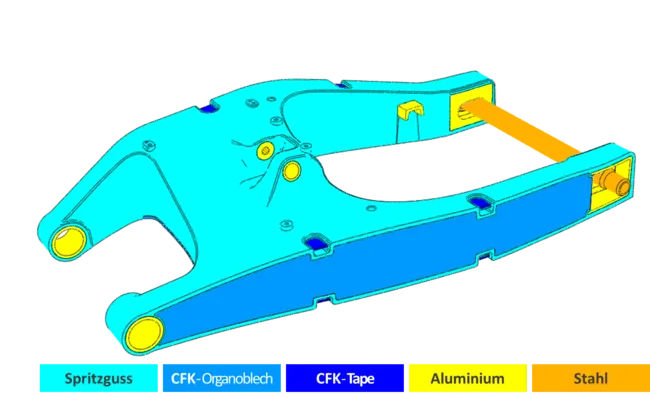
Method
Integral feature of the project was the establishment of a simulation methodology for threedimensional fiber reinforced components as part of a vehicle structure. Influences of the threedimensionally deformed vehicle structure as well as deformations of the carbon fiber reinforced material had to be taken into account. The work also covered the implementation of an automated manufacturing process including a suitable gripper solution and optical fault detection. Thereby, a widely automated process that considers requirements of the later serial production has already been achieved in the research stage. All results of the project led to the demonstrator of a motorcycle rear wheel rocker, which was tested under real conditions. All requirements of the project (e.g. consistently dynamically loaded part, no crash relevance, superposition of different fiber lengths as well as production processes that are cost-efficient and suitable for large-scale production) had to be met. The Chair of Carbon Composites explicitly adressed the integration of the bearing of the rocker, the connection to the suspension strut and the wheel bearings.
Acknowledgement
The chair thankfully acknowledges the funding of the project “MAI Hiras + Handle” provided by the German Federal Ministry of Education and Research under the leading edge cluster MAI Carbon (funding code: 03MAI27G).

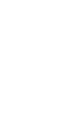
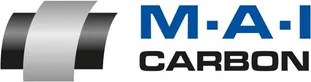
Contact Persons
Dr.-Ing. Swen Zaremba
Final Report
External link (pdf)