SUOMI – Automated Manufacturing of sustainable Sports products by combining bio-based Composite Materials and Digital Quality Inspection
Minimize waste, scrap, and material consumption while increasing the amount of bio-based material and reducing the environmental footprint through laser optical quality inspection and the production of an AFP-processable bio-based prepreg.
Project Partners
Walter Seikowsky GmbH, The Bakery Snowboards, Addcomposites, University of Bayreuth – Department of Polymers Engineering
Duration
01.10.2022 – 31.03.2025
Funding authority
Federal Ministry for Economic Affairs and Climate Action
Motivation
Nowadays, sports products are mainly manufactured by hand, which takes a considerable amount of time. In addition, there are large fluctuations in the final component quality, as no standardised and automated manufacturing process has been established. High-performance composite materials such as CFRP are already being processed in order to guarantee optimal performance of the components. The use of sustainable, natural-based materials such as bio-epoxy or natural fibres has only been sporadically tested so far. The so-called Automated Fiber Placement (AFP) process is currently mainly used in the aerospace industry and has not yet been established in smaller sectors such as the sports industry due to high investment and operating costs.
Method
The aim of the project is to automate the manufacturing process of lightweight sports products by optimally combining digitalisation and sustainability. In this project, an automated manufacturing process with integrated quality assurance is being developed using the example of a snowboard, which makes it possible to process newly developed bio-based materials. This enables shorter cycle times of up to 60 % and a reduction of CO2 emissions in production of up to 50 %. The AFP process offers the great advantage of robot-assisted material deposition on a tool along a defined path. With a suitable sensor integration, it is also possible to evaluate the depositing quality in real time. Through the development of a new low-cost AFP laying head with reduced working space, it will be possible to establish this automated manufacturing process in other areas as well.
Acknowledgement
The chair thanks for the support of the project "SUOMI", which was granted by the Federal Ministry of Economic Affairs and Climate Action under the heading "ZIM: Production Research".

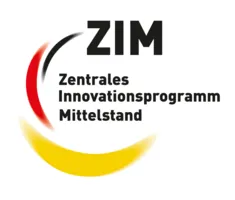
Contact Persons
Fabian Diemar, M.Sc.; Dr.-Ing. Swen Zaremba