SKR-FVK – Increasing Cost Efficiency and Robustness in the Automated Production of Fiber Reinforced Plastic Parts
Characterization and validation of a novel CRTM process variant at which the preform is encapsulated by thermoplastic films to reduce process cycle time and equipment investment costs.
Project Partners
Alpex Technologies GmbH, DEKUMED Kunststoff- und Maschinenvertrieb GmbH & Co. KG, RAC GmbH - Riedmann Advanced Composite, Polymer Competence Center Leoben GmbH, Chair of Carbon Composites - Technical University of Munich
Duration
01.10.2019 – 30.09.2021
Funding authority
German Federal Ministry for Economic Affairs and Energy as well as Austrian Federal Ministry of Digital and Economic Affairs
Motivation
The industrialization of fiber reinforced plastic (FRP) manufacturing processes has made it possible to competitively produce FRP structures in small to medium volume automotive production lines. However, process time analyses of commonly used FRP manufacturing techniques show that non-value-adding process steps, such as evacuation and tool cleaning, currently account for up to 30% of the total process time. With the aim of reducing the process cycle time, a new process variant based on the Compression Resin Transfer Molding (CRTM) process is being developed in the SKR-FVK project. The innovative approach of the "Film-Sealed Compression Resin Transfer Molding" (FS-CRTM) process is to encapsulate the preform with thermoplastic films. The film acts hereby as a sealing which prevents the resin from getting into contact with the mold during injection and therefore avoids tool contamination. The film-sealed preform can be evacuated outside the mold in an upstream process – also reducing press cycle time. Conventional sealing systems become redundant with FS-CRTM, allowing new mold concepts to be developed for FRP production. Additionally, an optimized CRTM process control allows to reduce process pressures, thus enabling a production with more cost-effective low-pressure injection machines and without cost-intensive presses. By developing the FS-CRTM process, the SKR-FVK project contributes to enhance FRP manufacturing processes and meet the high demands of large-volume automotive production.
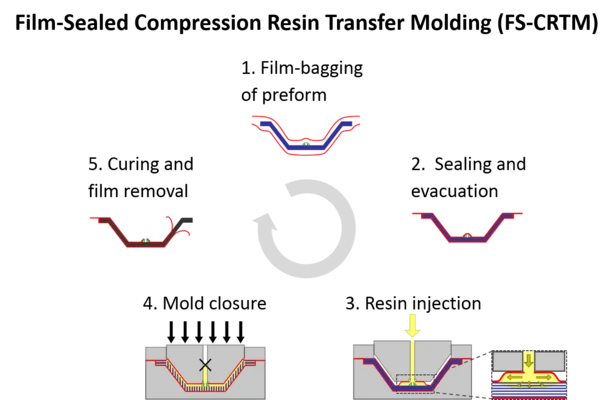
Method
Within the project SKR-FVK, the Film-Sealed Compression Resin Transfer Molding process is characterized at the TUM and its industrial feasibility is verified by laboratory experiments as well as by production of demonstrator parts. At the beginning of the project, dominant process parameters for a robust production are determined by laboratory experiments. The hereby used laboratory equipment has been specifically developed for this purpose. The test rig makes it possible to experimentally investigate both the injection and the compression phase of the FS-CRTM process and to record all important process parameters, such as injection pressure or compression force. The cavity is made of transparent PMMA, so that the impregnation can be recorded by cameras both on the top and bottom side of the preform. The hereby realized optical process monitoring system makes it possible to investigate potential causes of incomplete preform impregnation, such as racetracking, and to validate potential prevention strategies by using active flow control mechanisms. In the second part of the project, two- and three-dimensional demonstrator parts are produced using low-pressure injection systems and dynamic tooling systems, which are specially developed by project partners. The novel dynamic tooling system enables a FS-CRTM production without a cost-intensive press and additionally includes a movable tool concept (slide technology), by which on the one hand, complex component geometries with e.g. undercuts can be produced and on the other hand, the resin flow can be controlled via local preform compaction.
Acknowledgement
The chair thankfully acknowledges the funding provided by the German Federal Ministry for Economic Affairs and Energy (BMWi) under the scheme “Zentrale Innovationsprogramm Mittelstand (ZIM)” (funding number: ZF4004314TA9) as well as the Austrian Federal Ministry of Digital and Economic Affairs under the scheme “Coin-Programmlinie Netzwerke – international”


Contact Persons
Dr.-Ing. Swen Zaremba