MAI Tank – Development of an Efficient Manufacturing Technique for Innovative Pressure Vessels from Thermoplastic Composites for the Aviation Industry
Extreme lightweight design by means of new kinds of sandwich structures
Project Partners
Airbus Defence and Space GmbH, BASF SE, BMW AG, Foldcore GmbH, Neenah Gessner GmbH, Neue Materialien Bayreuth GmbH, SGL Carbon GmbH, Werkzeugbau Siegfried Hofmann GmbH
Duration
01.01.2015 – 30.06.2017
Funding authority
German Federal Ministry of Education and Research
Motivation
The extinguishing agent that has been used for many years on aircraft will be prohibited on new aircraft from 2018 on due to its environmental risks. As an alternative, nitrogen together with water spray shall be used. For the storage of nitrogen, lightweight pressure vessels are required. Within the framework of the project MAI Tank, new kinds of pressure vessels from carbon fiber reinforced plastic (CFRP) had to be developed and investigated. An efficient manufacturing technique of these vessels from thermoplastic CFRP was front and center of the project. The aproach of a serial manufacturing of pressure vessels, which had already been investigated in the project StorHy, was taken up and further developed in the new project. The use of a centrifugal process for the production of a type 5 tank was however a new aspect. Compared to pressure vessels that are already available on the market, the production process can be made more efficient and the tanks can be used in broader fields of applications due to the modular design of the vessels. Another advantage of the new process is that the required sealing layer can be joined with the laminate of the cylinder in one process step.
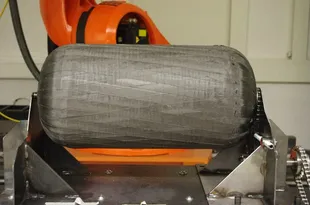
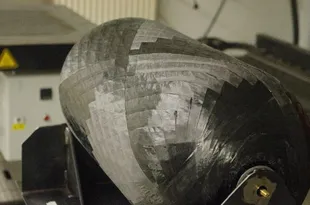
Method
For the selection of a suitable tape material, several tape specimens were thoroughly investigated. Grinding specimens were manufactured and the surface of the tapes was characterized. To establish suitable processing parameters, layup trials on the AFPT machine of TUM-LCC were conducted. The aim of these trials was to find a window of process parameters (temperature, velocity, consolidation pressure) that ensures a complete consolidation of the tapes. In order to quantify the consolidation quality, wedge-peel tests were conducted. Subsequently, the AFTP machine hat to be modified in order to enable a full coverage of the lateral metal connecting parts (boss parts) by tape material and in order to avoid collisions between the placement head, the tank and the winding axis. Based on an analysis of the machine, a new consolidation roller was designed and a freestanding winding apparatus was built. In the next step, the programming, deposition paths were created in Cadwind®. During the manufacturing of the tank, the circumferential layers could be placed without any problems. The selected process parameters lead to a very good consolidation of the layers. After the circumferential layers, several crossing layers were deposited. The cross layers both served as axial stiffeners to the tank and stabilized the lateral connecting parts in the liner. During winding of cross layers at an angle of 10° relative to the longitudinal axis of the tank, gaps between the connecting parts and the laminate were however observable.
The following causes for this defect were identified:
- The working principle of the ATP/AFP technology
- The relation of size of the placement head to the part
- The design of the lateral connecting elements and of the tank itself.
For an evaluation of the manufacturing concept, a burst test was conducted by VOITH. The tank failed in a catastrophic manner already at a pressure of about 150 bar. This was significantly less than the pressure of 900 bar, which the vessel was designed for. The burst test showed, that a lateral connecting element was pushed out of the laminate. This damage symptom confirmed the assumption that the not completely covered connecting parts were the weak point of the tank. The geometry of the liner and the design of the connecting parts were based on a common solution for tanks that are manufactured by wet filament winding. Thus, the design was only a compromise for the ATP process. Two basic approaches for the redesign of the tank are conceivable:
- Production ready design of the connecting parts for a better accessibility of the connecting parts by the placement head. This way, the connecting parts can be fully covered with layers of tape as it is the case during the filament winding process.
- Under the premise that the connecting parts cannot fully be covered by tape material, the connecting parts need to be mechanically redesigned so that the load caused by the inside pressure can still be carried, even under incomplete coverage.
Publications
Schäfer, P.M.; Guglhoer, T.; Sause, M.G.R.; Drechsler, K.: Development of intimate contact during processing of carbon fiber reinforced Polyamide-6 tapes. Journal of Reinforced Plastics and Composites, 2017, 1 – 15
Schäfer, P.M.; Gierszewski, D.; Kollmannsberger, A.; Zaremba, S.; Drechsler, K.: Analysis and improved process response prediction of laser- assisted automated tape placement with PA-6/carbon tapes using Design of Experiments and numerical simulations. Composites Part A: Applied Science and Manufacturing 96, 2017, 137-146
Schäfer, P.M.; Kreuzhage, S.; Zaremba, S.; Drechsler, K.: Experimental Investigation of inter-layer thermal contact resistance and its relevance for consolidation of thermoplastic composites. ECCM17 - 17th European Conference on Composite Materials, 2016
Schäfer, P.M.; Staden, M.; Zaremba, S.; Drechsler, K.: Material characterization for determining the consolidation properties of carbon fiber tapes with PA 6 matrix. ICCM-20 - 20th International Conference on Composite Materials, 2015
Acknowledgement
The chair thankfully acknowledges the funding of the project “Entwicklung eines rationellen Fertigungsverfahrens für neuartige Drucktanks aus Faser-Thermoplast-Verbunden für die Luftfahrtindustrie – MAI Tank” provided by the German Federal Ministry of Education and Research under the leading-edge cluster MAI Carbon (funding code: 03MAI24C).

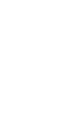
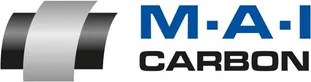
Contact Persons
Dipl.-Ing. Kalle Kind; Dr.-Ing. Swen Zaremba
Final Report
External link (pdf)