MAI Profil – Highly Loaded, Economical Hollow CFRP Profiles for the Automotive Large-Scale Production
The thermoplastic winding technology was further developed for smaller diameters by means of modifications of the placement machine and design rules for bonding of wound CFRP parts to the periphery were established (hybrid bonding).
Project Partners
Audi AG, CG TEC GmbH, CirComp GmbH, Munich Composites GmbH, Thermoplast Composite GmbH (early withdrawal)
Duration
01.08.2014 – 30.06.2017
Funding authority
German Federal Ministry of Education and Research
Motivation
Thin walled hollow profiles, like tubes or or pillars, can already be manufactured from carbon fiber reinforced plastic (CFRP). A well known example for this are high-end bicycle frames. However, current processing technologies only allow thin walled hollow profiles with constant cross sectional thicknesses. Moreover, these profiles are in general considerably more expensive than steel or aluminium profiles due to the types of carbon fibers and the manufacturing processes used. Within the framework of this project, these drawbacks of hollow profiles were adressed. Processes for manufacturing profiles with variable, locally reinforced cross sections and higher wall thicknesses were newly developed. In order to establish reasonable use cases for these new profiles, new methods for bonding them to surrounding components were required.

Method
Goal of the subproject of the Chair of Carbon Composites was to optimize the thermoplastic winding process towards smaller part diameters. Up to then, hollow profiles with an inner diameter in the range of 50 – 1300 mm and wall thicknesses of 0,2 – 40 mm had been realized using the thermoplastic winding technology. For a further reduction of possible diameters smaller than 30 mm, requirements regarding the treatment of the material and also the tool had to be adressed. This particularly included:
- Modifications of the laser optics and the closed loop control with a focal spot of 40x40 mm when useb on highly curved surfaces in order to avoid local overheating or insufficient heating.
- Adjustment of the process window in order to achieve a homogenious composite material.
- Modifications of the tool (consolidation roller) in order to realize high curvatures at different fiber orientations.
- Comparison of the material performance of thermoplastic in-situ consolidated material with already further developed thermoset materials and processes.
For the bonding of the CFRP parts and for load introduction, new joining technologies were identified and calculated. This particularly included the identification and establishment of new fiber composite specific joining techniques under consideration of possible manufacturing processes and other requirements. Questions regarding joining of different material types (hybrid joining) were particularly adressed. It was focused on a compression connector as an economically feasible joining technique. Moreover, techniques for load introduction from the periphery, e.g. by form closure, were investigated. Furthermore, a numerical calculation of the bonding area under consideration of the specified loads was carried out. From the results, design rules for the bonding area and the prediction of the joining strength were established.
Acknowledgement
The chair thankfully acknowledges the funding of the project “Hochbelastete, wirtschaftliche CFK-Hohlprofile für die automobile Großserie – MAI Profil” provided by the German Federal Ministry of Education and Research under the leading edge cluster MAI Carbon (funding code: 03MAI29F).

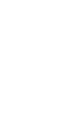
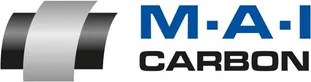
Contact Persons
Dipl.-Ing. Kalle Kind; Dr.-Ing. Swen Zaremba
Final Report
External link (pdf)