LEEToRB – Lightweight, Energy-Efficient Tooling for the Manufacturing of Rotor Blades
Plastics reinforced with fibre have already proven their potential for lightweight and more environmentally friendly aircraft. As a cost-effective technology for producing high-quality composite parts, resin transfer moulding (RTM) is a real improvement over open moulding, but new tooling materials are required to make the production process of parts less costly and energy intensive.
Project Partners
Qpoint Composite GmbH, Fraunhofer Institute for Casting, Composite and Processing Technology (IGCV), Airbus Helicopters GmbH
Duration
01.05.2013 – 30.09.2015
Funding authority
FP7-JTI - Specific Programme "Cooperation": Joint Technology Initiatives of the European Union
Motivation
The use of steel and metals as tooling materials has presented many challenges regarding the required energy and material input. Having also different properties from the fabricated composite part, they lead to deformation of the final part, which goes hand in hand with financial expenses. To address these challenges, the project LEEToRB proposed the use of carbon fibre as a tooling material instead. High strength and stiffness relative to their weight compared to metals was the reason for choosing composites as the material of choice. In addition, the low thermal mass leads to major reductions in energy use of up to 50 %.


Method
Our researchers successfully performed a proof-of-principle of their ideas by unveiling an RTM tooling based on fibre-reinforced plastic for production of helicopter rotor blades. To further enhance the production process and reduce energy consumption, the team integrated a heating device that introduced heat where needed. A carbon roving was used as an electric conductor and stitched to a glass fabric. When attached to an energy source, the carbon roving acted as resistive heating and, depending on its pattern, it adjusted the heat input. Stiffening ribs and a steel frame were applied on the back of the carbon fibre tooling shell to reduce the deformation caused by compaction and injection forces. The use of carbon fibre-reinforced plastic as the main material enabled lighter tooling devices in combination with more efficient heat-up and cooling. The newly developed prototype enables substantial savings in terms of energy input, from tool manufacturing to rotor blade production.
Publications
Weiland, Jakob Sylvester: Thermal Design of Resistively Heated Tools for Composite Manufacturing. Dissertation, 2017
Weiland, J.; Hubert, P.; Hinterhölzl, R.: Thermal dimensioning of manufacturing moulds with multiple resistively heated zones for composite processing. Journal of Composite Materials, 2017
Kammerhofer, P; Zaremba, S.; Drechsler, K.: Investigation of thermal ageing of advanced CFRP tooling laminate by gas permeability. ECCM17 - 17th European Conference on Composite Materials, 2016
Weiland, J.; Hartmann, M.; Hinterhölzl, R.: Cure simulation with resistively in-situ heated CFRP molds: implementation and validation. Composites Part A: Applied Science and Manufacturing, 2015
Weiland, J.; Hartmann, M.; Hinterhölzl, R.: Characterization and numerical investigation of an RTM cure process with CFRP molds and independent heat patches. ICCM-20 - 20th International Conference on Composite Materials, 2015
Kammerhofer, P.; Zaremba, S.; Drechsler, K.: Investigation on the mechanical robustness of CFRP molds. ICCM-20 - 20th International Conference on Composite Materials, 2015
Acknowledgement
This project has received funding within the framework of the FP7-JTI - Specific Programme "Cooperation": Joint Technology Initiatives of the European Union under grant agreement No 325936 (“Lightweight, Energy-Efficient Tooling for the Manufacturing of Rotor Blades”). This publication reflects only the author’s views and the European Union is not liable for any use that may be made of the information contained therein.
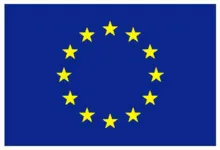
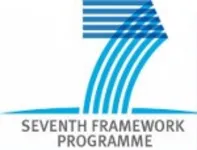
Contact Persons
Dipl.-Ing. Kalle Kind; Dr.-Ing. Swen Zaremba
Final Report
Download (pdf)