ENGINEERED – Development of a phenomenological material model for simulative description of the post-fracture behavior of composites
Test methods and micromechanical models for the characterization of the post-fracture behavior of composite materials are developed which serves as base for the development of a module for the phenomenological material model MF GenYld+CrachFEM for crash simulation.
Project Partners
MATFEM Partnerschaft Dr. Gese & Oberhofer
Duration
01.10.2020 – 31.03.2022
Funding authority
Federal Ministry for Economic Affairs and Energy
Motivation
Composite materials show high values for specific energy absorption, which is advantageous for crash structures. For the use in automotive or aerospace applications a reliable design using numerical analysis is needed. Current material models do not show the same robustness and accuracy as models for metallic materials. To acquire further lightweight design potential by the use of composites, material models that are capable of a precise description of the complex failure behavior are required. A key factor for that is the investigation of the post-fracture behavior. Currently there exists no standardized methodology for the characterization of this.
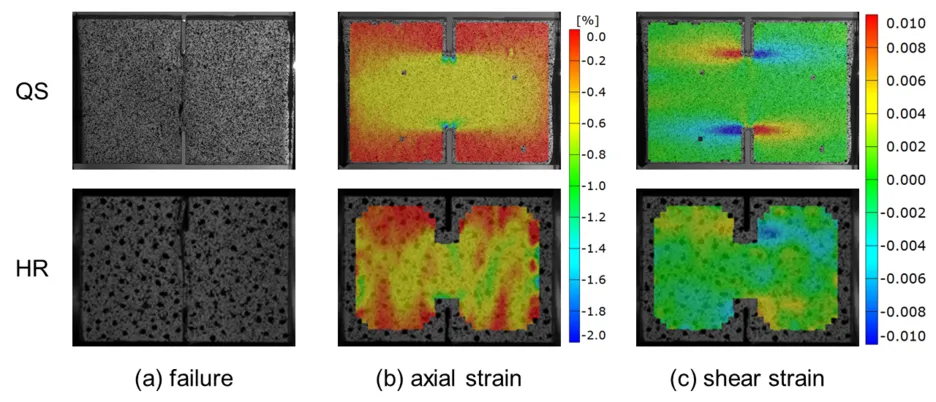
Method
TUM-LCC carries out a comprehensive characterization of the inter- and intralaminar failure behavior of a glass-fiber composite in dependence on loading direction and rate. An aim is to contribute to the standardization of the characterization of fiber-reinforced composite crash structures. Furthermore TUM-LCC will develop micromechanical models to investigate the potential replacing of physical tests by virtual tests to reduce time and cost intensive test programs. The project partner MATFEM will integrate the characterized post-fracture behavior into the material model MF GenYld+CrachFEM as an additional module that finally will be validated in component tests.