DeMAnD – Dynamic Aircraft Material Property Database
The DeMAnD project has been set up to carry out a mechanical material characterization program to deliver a dynamic material property data base for typical aircraft materials, with a special focus on seat and crash absorbing structures of small aircraft.
Project Partners
German Aerospace Center, INEGI - Institute of Science and Innovation in Mechanical and Industrial Engineering
Duration
01.09.2016 – 31.03.2018
Funding authority
Clean Sky 2 Joint Undertaking under the European Union’s Horizon 2020 research and innovation programme
Motivation
The objectives of the DeMAnD project were as follows: 1. Determination of strain rate dependent material behaviour for typical structural aircraft seat and crash absorber materials (metal alloys, fiber-reinforced polymer composites, foams). 2. Efficient, yet complete coverage of strain rate regimes ranging from quasi-static loading up to strain rates of 500 s-1. 3. Development of new specimen geometries and methodologies, most suitable for the dynamic loading of the materials selected in the project. 4. Determination of the complete stress-strain response for the materials and strain rate regimes selected in the project. 5. Determination of strain rate trends for relevant material properties (e.g. modulus, strength and failure strain, if applicable).
Method
The main results obtained in the project were: 1. The size effect study (comparison of static tests with specimen geometries defined by respective ASTM standards and small specimen geometries required for the strain rate dependency study), showed that the reduced specimen geometries yielded a representative mechanical response and are therefore applicable for further testing at higher strain rate level for all materials and test types. 2. No significant strain rate sensitivity was measured for the metal materials selected in the project. 3. No significant strain rate sensitivity was measured for the Carbon SMC composite material. 4. Significant strain rate effects were measured for the carbon and glass fabric composite test series, with exception of 0° tensile loading of carbon fabric, where no strain rate effect was observed. 5. The crushing stress-strain response of the foam material exhibited an obvious strain rate effet. A quantative anaylysis of the strain rate effect was not possible, due to differences in the stress-strain response of the available foam material (test panels). The following progress beyond the state of the art was reached: 1. Despite the fact that no significant strain rate dependencies were observed for the metals, the results are unique, since they cover a wide range of metal alloys and were all done with the same setup (generally dynamic material properties need to be "gathered" from different publications, making a direct comparison difficult). 2. The results obtained for the Carbon SMC are new and unique and shall be published in an international journal. 3. The completeness of results obtained for the fabric composites is unique and valuable (carbon and glass fibers, 0° and 90° tension and compression).
Publications
M. Ploeckl; D. Schüler; S. Pourhassan; P. Moreira; H. Koerber; High strain-rate behavior of sheet molding compounds under tension, compression, and shear loading. International Conference on Composite Structures 20 4th – 7th of September, Paris
Acknowledgement
This project has received funding from the Clean Sky 2 Joint Undertaking under the European Union’s Horizon 2020 research and innovation programme under grant agreement No 717172. This publication reflects only the author’s views and the European Union is not liable for any use that may be made of the information contained therein.
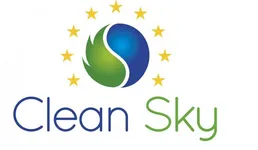
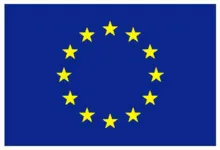
Contact Persons
Luciano Avila Gray, M.Sc.; Dr.-Ing. Swen Zaremba
Final Report
Download (pdf)