In order to achieve the goals for environmentally friendly aviation, the aviation industry must find energy-efficient and resource-saving solutions not only for the end products but also for their production. Composite materials such as carbon fiber reinforced plastics (CFRP) offer enormous lightweight potential for structural components of aircraft, which increases their environmental compatibility. Established manufacturing processes for CFRP components are, however, characterized by high energy consumption, for example during cooling of the pre-impregnated semi-finished products (prepregs) and curing in the autoclave.
In the joint project "InLineCon", the University of Bayreuth and the Technical University of Munich are therefore aiming at a material and process development that will eliminate the steps of prepreg cooling and consolidation in autoclaves required for thermoset systems. This involves the production of a radiation-curing and thermally fast-curing resin system or the combination to form dual-curing formulations. By this, the energy-intensive continuous cooling chain at -18 °C that is usual for prepregs is no longer required. The manufacturing process used is Automated Fiber Placement (AFP), which is well established in the aerospace industry. In InLineCon, the AFP machine and the process are modified in such a way that in-line consolidation of the newly developed resin system directly in the lay-up tool becomes possible. Eventually, the process time in the autoclave required for composites can be minimized or even completely avoided by an appropriate temperature and pressure profile.
The project is supported under the scheme Federal Aeronautical Research Programme (LuFo) by the German Federal Ministry for Economic Affairs and Energy.
News
Fundamental research on the direct consolidation of thermoset prepreg tapes using Automated Fiber Placement
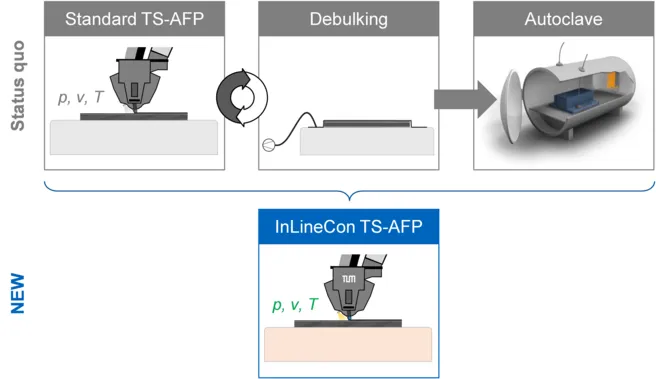