The TS-AFP system from Coriolis Group SAS in Quéven, France, is an automated fiber placement system with two main elements. A tape-laying head, controlled by a KUKA robot, conveys, cuts, and places thermoset-prepreg-slit-tapes on the mold surface. The other main component is the creel, where the prepreg material is stored during the process.
Using two infrared emitters and a tilting compacting roller enables a bidirectional laying process that increases productivity. It can process very narrow tapes, producing smaller and more complex 3D-double curved parts and steering radii of up to 400 mm can be realized.
The line is versatile and can process various materials, including conventional and UV-based resins. Multiple tools can be integrated between the rotary axes of the system, which also realizes the winding of components. A wide range of parts can be produced, from rotationally symmetrical to sandwich structures with three-dimensional curvatures with ramp angles of up to 35°.
A laser light-section sensor from InFactory is attached to the AFP layup head for quality assurance. It can generate gray-scale images and point clouds of the laid-up tracks. Research approaches are available for automated evaluation routines for gray-scale images and point clouds.
Technical details
• No. of tapes: 8
• Tape width: 1/8‘‘
• Heat source: IR emitter
• Max. IR emitter power: 430 W
• Max. compaction force: 500 N
• Min. tape length: 63 mm
• Max. lay-up rate: 0,5 m / s
• Lay-up direction: bidirectional
• Max. component: 1459 mm x 909 mm
• Min. steering radius: 400 mm (lt. Anlagen-Datenblatt 900 mm)
• Max. ramp angle: 35°
Contact person
Nils Siemen, M.Sc
The tape laying systems for direct consolidation of fiber reinforced thermoplastic tapes is from AFPT GmbH in Dörth. By using a robot-guided laying head, the load-path deposition of fibers with near-net-shape components and complex geometries can be achieved with minimal waste. In the process, the matrix of the incoming tape and the already deposited substrate are brought to a molten state using a heat source (LED laser). The incoming tape is then welded to the substrate while pressed onto the tool using a consolidation roller.
Technical details single tape winding and placement head
• Table size in length x width [mm]: 1200 x 1200
• Heated table size (max. 300°C) length x width [mm]: 650 x 650
• Winding axis Diameter range [mm]: 15 – 1300
• Tape width [mm]: 10 – 52
Technical details vessel winding head
• Winding axis diameters [mm]: 15 – 1000
• Heated table size (max. 300°C) length x width [mm]: 50 – 3000
• Tape width[mm]: 10 – 25.4
Contact person
Dipl.-Ing. Vincent Backmann
The filament winding machine from Hille is a 5-axis CNC winding machine for depositing rovings on a rotating mandrel. The machine is primarily suitable for the production of rotationally symmetrical structures such as tanks or pipes, but plates for material characterization or non-rotationally symmetrical tanks can also be produced. However, components with concave geometry cannot be produced in the winding process.
The system has two unwinding stations, an impregnation unit, yarn tension control and five axes for precise positioning of the fibers on the winding core. The system is versatile and can process various materials such as dry fibers, conventional wet winding resins, towpregs and slit tapes. A drum impregnation system and a dip impregnation system are available for bringing the fibers in contact with the matrix resin. The impregnation bath can be heated in the temperature range from 25 to 120°C, for instance to adjust the viscosity of the resin. The impregnation unit can be removed when processing pre-impregnated semi-finished products like towpreg. A roving heater, a UV lamp on the pay-out head and a thread brake are optionally available on the machine and enable the processing of a wide range of materials.
Technical details
• Max. component length: 2,600 mm
• Max. component diameter: 700 mm
• Number of unwinders: 2
• Thread tension: 3-80 N
• Tempering range impregnation bath: 25 - 120 °C
• Heating capacity impregnation bath: 1.5 kW
Contact person
Elisabeth Gleis, M.Sc.
The maypole braiding machine enables the production of braided semi-finished products as well as the direct production of preforms using the overbraiding process. Different reinforcing fibers such as glass, carbon or aramid fiber can be used. The system has a quality assurance system developed at the LCC that can detect possible problems before the yarn breaks. A KUKA KR210 L150-2 industrial robot is available for overbraiding. The system can be swiveled horizontally, for example to suppress the influence of gravity on the braid formation.
Technical details
• Number of bobbins: 128
• Number of Horngears: 32
• Type of braids: round, flat
• Direction of reinforcement fibers: biaxial, triaxial, unidirectional
• Interlock: 1 x 1, 2 x 2, 4 x 4
Contact person
Dipl.-Ing. Kalle Kind
Desktop-sized complete filament production line packed into one desktop sized machine making it possible to produce spools of own custom 3D-printing filament out of pellet-sized or shredded thermoplastics.
Technical details
• Suitable for PEEK, PEI etc.
• Temperature peek point: 450°C
• Material mixing screw
• Filament diameter range: 0.5-3 mm
Contact person
Bernhard Bauer, M.Sc.
The Anycubic Photon Mono M5s is an MSLA 3D printer for the production of highly detailed structures. It is easy to use thanks to its automatic bed leveling and automated resin quantity check. With the help of various UV resins, different material properties from flexible soft to high temperature resistant can be set. The 10.1” screen enables the production of larger structures.
Technical details
• Build volume: 200x218x123mm(HWD)
• Resolution: 12K (11,520 x 5,120px)
• Print speed: up to 105mm/hr
Contact person
Maximilian Konstantin Strobel, M.Sc.
The AM Flexbot from the Dutch company CEAD is a large format 3D printer. A robot can either grab: the extruder for the additive manufacturing of e.g. operating equipment, composite tools or structural components, a milling spindle for e.g. subsequent surface processing, or currently an ATLAM pilot system for the integration of continuous fibers in the additive manufacturing process. A wide variety of thermoplastic polymers such as PP, PA6, PESU, PEEK etc. (with and without short fibers) can be processed. A material dryer, control of the robot via Siemens Sinumerik and a probe tool for measuring components contribute to high quality.
Technical details
• Printing temperatures up to 450°C
• Material output rates up to 10 kg/h
• Print area up to 3 x 1.2 x 1.2 m (L x W x H)
• Milling with up to +-0.2 mm accuracy possible
Contact person
Matthias Feuchtgruber, M.Sc.
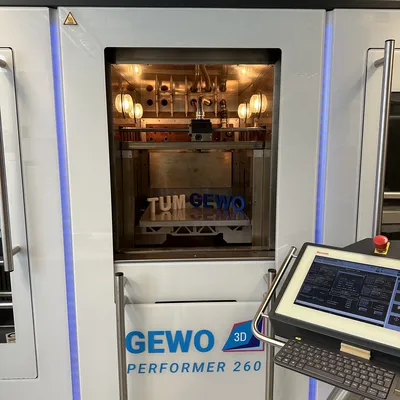
The GEWO Performer 260 is a special development for industrial additive manufacturing. High-performance thermoplastics like PEEK or PEI can be printed due to a heated printing chamber, as well as highly filled filaments with fiber content. The filaments can be stored in an integrated filament drying unit. Four printing heads allow multi-material prints during one print job. Due to an automated cleaning system, the contamination and mixing of materials can be prevented with every tool change.
Technical details
• Print chamber: 450 x 450 x 350 mm (L x W x H)
• Nozzle temperature up to 450 °C
• Print chamber temperature up to 260 °C
• Print bed temperature up to 270 °C
• Material output rate up to 0,5 kg/h
• 4 print heads
Ansprechpartner*in
Melike Kizak, M.Sc.
The multi-head printer, housed within a mobile safety cell, is a robotic 3D printer that is able to produce both large-scale components and continuous fiber-reinforced parts. It consists of a KUKA KR30 6-DOF industrial robot equipped with two print heads: the Dyze pellet extruder and the Anisoprint continuous fiber co-extrusion printhead. With its 6-DOF configuration, the robot offers the advantage of printing in a nonplanar manner, expanding the range of possible applications.
Technical details
• Robot: KUKA KR30
• Controller: KUKA KRC4
• Printheads:
o Anisoprint co-extrusion printhead
o Dyze pallet extruder
• Print area: 1000 x 800 x 500 mm (L x W x H)
• Print bed temperature: up to 270 °C
Contact person
Chih-Yu Chen, M.Sc.
The Prusa i3 MKS3+ is a desktop 3D printer for the rapid production of auxiliary equipment for research at the LCC. Its compact design allows us to operate 4 printers in a small space. Thanks to the simple operation and the PrusaSlicer developed by Prusa, the system can be learned to operate in just a few minutes. Printable materials are PLA, ABS up to PA6 with 20% carbon fiber content.
Technical details
• Construction volume: 25×21×21 cm
• Layer height: 0.05 - 0.35 mm
• Max. Temperature: 300°C
Contact person
Maximilian Konstantin Strobel, M.Sc.
The Towpreg machine TLM 2.4, developed by Roth Composite Machinery GmbH, is designed to facilitate the automated impregnation of carbon fibers with thermosetting epoxy resins. It allows the processing of rovings with a titre ranging from 400 to 3600 tex and the impregnation of carbon, glass, flax, basalt fibers, etc., with resin systems suitable for Towpregs. The system is equipped with 4 cross winders and 1 parallel winder to wind Towpregs according to specific requirements and applications.
Technical details
• Max. production speed: 110 m/min
• Simultaneous impregnation of up to four rovings
• Viskosity range 1000 – 10.000 mPas
• Processing with release film is possible
Contact person
Youssef Mraidi, M.Sc.
This infusion system is specifically designed for infusing reactive resins (e.g., RTM6) in composite applications. It enables precise dosing of resin systems through an integrated scale, operating at temperatures of up to 120°C. The system can regulate pressure between -1 and 6 bar and controls the infusion process using pinch valves. Additionally, it features two heated lines to ensure the optimal temperature throughout the infusion process.
Technical details
• Container Size (DxH): Ø250mm x 350mm
• Pressure: -1 to 6 bar
• Max Temperature: 120°C
Contact person
Youssef Mraidi, M.Sc.
The 1-k pressure pot system is able to precisely dose reactive and non-reactive one-component systems. The can be controlled via an integrated scale and the injection pressure. The material can be degassed directly on the machine. The material can be sheared during processing using an integrated agitator.
Technical details
• Maximum injection pressure: 8 bar
• Heating of the pressure pot up to 160°C, injection hose up to 220°C
Contact person
Dipl.-Ing. Kalle Kind
Various dosing and mixing machines are available for processing highly reactive multi-component resins.
Technical details
• Injection pressure up to 20bar
• Precise dosage of up to three components
• Different mixing technologies (static, dynamic, ultrasound)
• Wide range of mixing ratios and viscosities can be processed
• Precise temperature control
Contact person
Dipl.-Ing. Kalle Kind
The 1-K RTM system is able to precisely dose reactive and non-reactive one-component systems volumetrically. Flow rate and maximum pressure are adjustable.
Technical details
• Temperatures on the piston and hose can be independently set up to 130°C
• Possibility of degassing using vacuum
• 10bar injection pressure
Contact person
Dipl.-Ing. Kalle Kind
The Rucks KV289.00 is a heated press for plastics processing. The press unit has elecitrcal heating and water cooling. The preheating unit consists of an IR emitter and a fixture or transport device that moves 2D blanks from the preheating station into the workspace of the press. This enables thermoforming of thermoplastic blanks, e.g. made of carbon fiber reinforced PEEK.
Due to the special construction, the working space of the press unit is only accessible from one side. The lower press plate can be deployed in front, in order to install a tool by using a crane.
Technical details (press unit)
• Max. press force: 3200kN
• Max. allowable field pressure: 25MPa
• Max. temperature: 400°C
• Press field size: 1200 mm x 800 mm
• Max. stroke: 770 mm
• Max. heating rate: 10 K/min
• Cooling rate: 5…15 K/min
• Max. speed opening/closing: 100 mm/s
• Max. press speed (2-5 mm/s), pressure-controlled
Technical details (preheating unit)
• Field size: 1500 mm x 1300 mm
• Max. temperature: 400°C
• Heating power: 1.5 W/cm²
• Adjustable offset between blank fixture and lower press plate: 0…270 mm
Contact person
Dominik Boos, M.Sc.
The Pinette vacuum press from PEI is a laboratory press for the production of coupons or small demonstrators. The special features of the press are the maximum pressing temperature of 500 °C and the sealable press chamber, which can be evacuated to approx. 10 mbar using a vacuum pump. Various composites with thermoset and thermoplastic matrix (e.g. PEEK) can be processed.
Technical details
• Max Force: 100 t
• Press Field: 600 x 600 mm
• Stroke: 400 mm
• Max. Temp: 500 °C
• Cooling Rates: 10 °C/min (0-250°C), 3.5 °C/min (>250°C)
• Vacuum: 10 mbar
Contact person
Jan Teltschik, M.Sc.
The Chair of Carbon Composites is equipped with a Vötsch Hephaistos VHM 180-200 microwave system. Microwave technology enables energy-efficient heating of parts and thus represents an alternative to conventional oven systems. By using microwave-absorbing materials, selective heating can also be achieved. The system has a hexagonal design with an inner diameter of 180 cm and a depth of 200 cm. The system consists of two modes with 12 magnetrons each, with each magnetron having a nominal power of 1 kW. The temperature control is realized by fiber-optic temperature sensors, and the entire chamber is monitored by thermography.
Technical details
• Frequency 2,45 GHz
• 24 magnetrons a 1kW
• Nominal temperature: 300 °C
• Maximum temperature (2nd limit): 800 °C
• Installation space: hexagonal 180 cm x 200 cm
Contact person
Maximilian Steinhardt, M.Sc.
Different ovens are used for processing and material characterization.
Technical details
• Voetsch VTL 275/250/350-250°C
o Usabel Size: 2750 x2500 x3500 mm
o Max Temp: 250°C
• Binder MKF 56 Dynamic Climate Chamber
• Various Ovens with Different Capabilities such as Vacuum or High Temperature
Contact person
Dipl.-Ing. Kalle Kind
The Zünd M-1200 flatbed cutter is used to cut materials arranged on the cutting table. CAD/CAM files in DXF format can be read in and processed. The following materials can be cut: dry carbon/glass fiber as textiles, prepregs, honeycomb, foils, rubber, leather, foams, adhesive foils, cardboard, paper. The cutter also has two different blade types for optimized use: a rotary blade for high processing speed and for cutting large radii and an oscillating blade for thick and tough materials. The cutter also has a vacuum unit that prevents the layers from slipping during the cutting process.
Technical details:
• Working area (Y x X): 1300 x 1200 mm
• Max. Cutting width in Y: 1200 mm
• Max. Cutting length in X: Theoretically infinite
• Max. Cutting height: 20 mm
• Bar height: 30 mm
• Speed: 1-1000 mm/s
• Accuracy: 0.01 mm
• Repeat accuracy: 0.04 mm
• Repeat accuracy in practice: 0.08 mm
• Weight: 370 kg
Contact person
David Faron, M.Sc.
Universal granulator for shredding solid, soft to brittle and tough plastics such as PP, ABS, PA, PC, etc.. The system is suitable for recycling short-fiber-reinforced plastics, which can be reprocessed as recyclate in a following production process such as granulate-based 3D printing.
Technical details
• Grinding chamber: 250 x 385mm
• Motor power: 7.5 kW
• Sieve sizes: 4, 5, 6 mm
• Dedusting and sound insulation integrated
• Throughput: approx. 120 - 200 kg/h
Contact person
Bernhard Bauer, M.Sc.