Autonomous Rotorcraft for Extreme Altitudes (AREA) in Synchropter (Flettner) Configuration
Brief history of the AERA Drone
The civil research project Autonomous Rotorcraft for Extreme Altitudes (AREA), which was conducted as a collaboration between TUM, DLR and Bauhaus Luftfahrt, aimed to develop a lightweight rotary wing UAVs for applications at high altitudes of up to 9000m, such as search and rescue as well as different types of environmental monitoring. Up to now, such rotary wing UAVs have not been available. Consequently, experience in design and operation of rotary wing UAVs in such environments is lacking. This situation motivated our team from DLR and TUM to work on an all-electric prototype of this kind of rotary wing UAV.
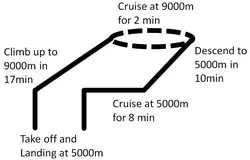
The challenge of designing a rotary wing UAV with available batteries (2015) and a maximum take-off weight of approximately 40kg demands the complete system to be extremely efficient over the whole mission profile. With regard to the rotor this means low values of blade loading at sea level are necessary, reducing power and retarding the onset of stall at higher altitudes. Compared to a conventional helicopter with main and tail rotor and the same disc loading, dual rotor configurations while hovering or at low speeds generally require less power for a given thrust. Therefore it is decided to design a Fletter type helicopter with intermeshing rotors. In addition to meet the extreme requirements for the UAV, rotor blades are designed, tested and built at TUM.
The project was supported by a MunichAerospace scholarship.
Keywords: High Altitude Helicopter Drone, Hubschrauberdrohne, Flettner, Synchropter.
The AREA drone is going to be modified with a hydrogen propulsion system:
_________________________________________________________________________________________
AREA Flight Test at 2830m MSL (41 different flights with different rotor speeds and gross weights were made on 2018-11-08)
Flight Tests for Model Validation with automatic Doublet and Step Inputs, 900ft/min vertical climb demonstration
Succesfull first hover test of a pre prototype with off the shelf parts
On June 19 2015, the first hover flight tests with a pre prototype (with mosty off the shelf parts) were performed. The all-electric system was operated at design configuation. But it emerged that the off-the-shelf parts do not satisfy our requirements. Thanks a lot again to SwissDronesAG for conducting the flights!
Combined tensile & bending test for the AREA rotor blade
On March 23 2015 a combined tensile and bending test for the self developed AREA rotor blades was made. Great thanks to Prof. Baier and Mr. Krämer from the Institute of Leightweight Structures for their great support.The requirements for limit and ultimate load are by far exceeded once again.
Production of the first rotor blade for the AREA-Project
A first rotor blade prototype has been demolded on January 20th 2015. We would like to thank the Institute for Carbon Composites for the support during the manufacturing of the rotor blade.
AREA first flight with off-the-shelf blades and gearbox
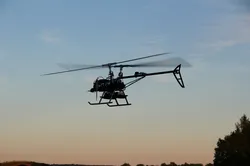
A first flight was conducted on July 1st 2014. The flight was intended to perform system and control checks. The prototype hovered for 2x12min in an altitude of 10m above ground.
Projektpartner
Deutsches Zentrum für Luft- und Raumfahrt (DLR)
Robotics and Mechatronics Center, RMC
Institute of Robotics and Mechatronics
www.dlr.de/rm